
Barrel fluting doesn’t just look cool, it has practical benefits too. This LWRC barrel is 20% lighter and cools faster.
The beautiful thing about building your own rifle is that you can be really, really picky about what components you choose. It’s your rifle, and you’re building it for your specific purposes so you can optimize each and every part according to your intended use of the finished product.
While numerous components and the assembly and fit thereof, have a big impact on finished rifle performance, it’s the barrel that’s gonna matter – a lot. You can make other decisions for less expensive components that can easily be upgraded later, but you’ll want to start with just the right barrel up front.
Type of Rifling
Choosing a rifling method for your ideal barrel is mostly an issue of personal opinion. People will battle to the death over whether button-rifling is better than cold hammer forged rifling and so on. I won’t go there as I’ve yet to see definitive proof that one method is demonstrably better than another for making AR rifle barrels. With that said, you’ll find that other types of rifles, like super-precise bench rest bolt-action models, will usually have cut or button rifling. Lot’s of folks will argue that when ridiculous accuracy levels are the goal, the button and cut methods excel.
Let’s take a look at various types of barrel construction, then you can make an educated choice as to which type floats your boat. Remember, we’re talking about applicability to AR rifles here, so factors like barrel longevity and heat tolerance might factor higher than pure accuracy in the pros and cons evaluation.
Cold Hammer Forged Rifling
The cold hammer forged method includes a lot of loud noise and violent pounding. As a result, it requires huge capital investments in machinery. It’s not like you can use this method with a hand-held mini-sledge: a giant hydraulic machine hammers the barrel blanks from all sides as the barrel passes through. Generally, companies that make a lot of barrels, like Daniel Defense and Smith & Wesson, will use the cold hammer forging technique as they can afford the capital investment.
A barrel blank with an oversized hole drilled for the bore is filled with a mandrel that is shaped like a mirror image of the inside of the bore. Imagine stuffing Play-Doh into a barrel, and somehow getting it out intact. That’s the idea of a mandrel. The mandrel is inserted into the bore, and as both are slowly pulled through, massive hammers pound the snot out of the outside of the barrel. This hammering forces the barrel blank to cave in and assume the exact shape of the mandrel.
One benefit of cold hammer forging is that it’s possible to create smooth polygonal rifling patterns. Some people like the small velocity advantage and smooth engagement of the more rounded polygonal pattern. This method stresses the steel more than other processes, and post forging heat treatment may be required to de-stress the steel, but that will happen before you ever receive the part.
Button Rifling
Button rifling also relies on brute force, but it’s done from the inside. The barrel blank has a hole that’s ever so slightly smaller than the finished product. A hard steel button is pulled (or sometimes pushed) through the bore with great force while the button is turned to create the spiral rifling pattern. The shape of the button literally compresses the rifling grooves into place. Brute force baby!
Button rifling methods also produce very smooth, hard and polished bores, as steel is pressed into the desired shape rather than tooled or cut.
Broach / Cut Rifling
Think of broach cut rifling as carving of the interior shape. A long rod has multiple cutting bits of increasing size spaced at intervals along the rod. The rod is pulled through the bore while being turned. Each bit cuts a little deeper, with the last bit on the rod creating the final groove dimensions.
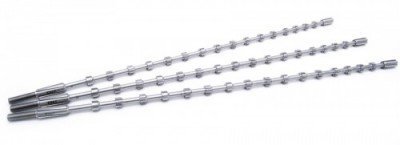
These Kingsford broach cutting tools have multiple cutting blades, each larger than its predecessor.
Barrels can also be cut with a single blade rather than a broach tool. Obviously this method is slower and requires multiple cutting steps, so it’s a more expensive process. Some high-end barrel makers swear by the method, however.
Cutting methods result in sharp rifling with well-defined grooves. Some folks think cut rifling can wear quicker due to the sharp interior surfaces.
Electrolysis Rifling
With this high-tech method, strips of desired shape are placed inside the bore while the whole assembly is submerged in a salt solution. Current is applied and the “wet etching” process eats away metal in the desired areas to produced rifling grooves. I’m not seeing a lot of this yet, but who knows what the future will bring?
Got something to say?