
Got leather?
Got cows?
Galco does. Lot’s of them. You know Galco, right? They’ve served billions and billions of holsters. Well, maybe not billions, but at least dozens of boatloads, judging by the size of their factory and activity level of all the folks in there.
I recently had the distinct pleasure of a factory tour. You see, I’m a self-admitted holster geek. I even wrote an entire book on methods of concealed carry and gun holsters. Yes, I’m hopeless on holsters, so when I had the opportunity to visit Galco, I jumped on it like Kanye West to the nearest microphone.
The very first thing I learned about was cows. Did you know that every year, Galco turns 886,000 square feet of leather into first-rate gun holsters? That’s about 20,000 cows. If you lined all those cows up, they would reach from PETA’s headquarters in Washington DC all the way to the Chick-Fil-A in Warrenton, Virginia. Trust me, I did the math.
OK, so odds are you’re not reading this because you need to know how many cows it takes to block the highway from DC to Warrenton, so let’s get to the cool part – the making of holsters. It’s a fascinating mix of high-tech automation and skilled hand crafting.
The first challenge is shoes. See, we used to make lots and lots of shoes here in the US, so there were thousands of tanneries that supplied all that leather. Now, since most shoes are made overseas, there are only two major vegetable tanneries here in the US, and Galco buys the lion’s share of tanned leather from both of them.
Like yummy steaks, leather comes in different cuts depending on the intended usage. Galco orders back sections, which are about half a cow from the center of the back down each side. One of these sections is about the size of the hood of a 1970 AMC Gremlin, but not quite as wide and a little longer.
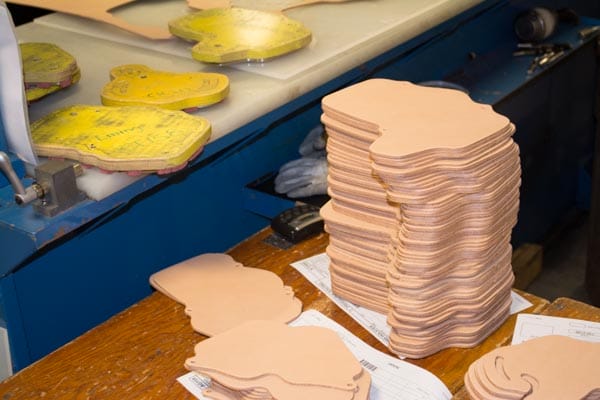
The handmade dies (upper left) are mashed through the leather sheets to produce desired shapes.
The older way of cutting leather involves use of hand-made dies. These dies are laid out over a sheet of leather and pressed through to cut the desired shape. It’s up to the experienced cutter to obtain maximum use of each sheet of leather while minimizing waste.

High-tech cutting. The leather is optically scanned to capture shape and flag areas of imperfection.
The new way is incredibly cool. As each cow is different, the incoming leather sheets are always different sizes. Imperfections such as discolorations or scrapes exist in different spots on each and every sheet. A digital scanner looks at each incoming sheet of leather and identifies shape, surface area and “marks” imperfection areas with a “do not use” status.
Got something to say?